1Menjong Sorig Pharmaceuticals Corporation Limited, Thimphu, Bhutan
Corresponding author: Sherab Tenzin, Menjong Sorig Pharmaceuticals Corporation Limited, Thimphu, Bhutan.
Email: sherabtenzin@mspcl.bt
DOI: https://doi.org/10.47811/bsj.0020060102
ABSTRACT
This article describes the integration of Quality Management Systems and Good Manufacturing Practices in the production of traditional medicines at the Menjong Sorig Pharmaceuticals Corporation Limited, a state-owned traditional medicine manufacturer in Bhutan. Rooted in Sowa Rigpa principles, the organization has adopted modern pharmaceutical standards to ensure the safety, efficacy, and quality of its products. Key components of Menjong Sorig’s Quality Management Systems include leadership commitment, risk-based preventive action, robust documentation, supplier qualification, personnel competency development, and stringent quality control. The alignment with ISO 9001:2015 standards and the principles of Good Manufacturing Practices underscores Menjong Sorig’s commitment to sustainable practices, from sourcing medicinal plants to ensuring compliance with regulatory requirements. Sustainable sourcing of medicinal plants is supported by good agricultural and collection practices and community-based initiatives. Stringent quality control measures, such as the use of High-Performance Thin Layer Chromatography , ensure that raw materials, intermediates, and finished products meet predefined quality standards. Menjong Sorig’s investment in personnel training and competency development reflects a commitment to continual improvement, with regular internal audits reinforcing compliance with global standards. Balancing traditional values with modern corporate expectations, Menjong Sorig has maintained stakeholder trust through transparent operations and adherence to regulatory requirements. This article highlights Menjong Sorig’s systematic approach to integrating traditional practices with modern pharmaceutical standards, setting a benchmark for quality in traditional medicine manufacturing. Menjong Sorig’s efforts exemplify a sustainable and innovative approach to preserving cultural heritage while ensuring the global relevance of traditional medicines.
Key words: Complementary Therapy; Healthcare Quality Assurance; Herbal Medicine; Patient Safety; Quality Improvement; Bhutan
INTRODUCTION
Menjong Sorig Pharmaceuticals Corporation Limited (MSPCL), established in 1998, serves as the cornerstone of
Traditional Medicine (TM) production in Bhutan. The organization has transitioned from manual medicine production to adopting
modern mechanized processes aligned with Good Manufacturing Practices (GMP) and other quality management principles [1, 2].
Its production philosophy balances the sanctity of traditional methods with the efficiency of contemporary technology,
ensuring that the core essence of Sowa Rigpa is preserved. Menjong Sorig produces over 123 essential TM formulations and
various herbal health supplements and caters to 22.9 – 28.4% of Bhutan's population that have been reported to avail TM services
[3, 4].
However, despite its advancements, MSPCL faces
significant challenges both in terms of operational
and regulatory barriers. Since the quality-assurance
elements are not built into the design of the manufacturing
facility, it is difficult to incorporate and fulfil
critical GMP requirements such as Heating, Ventilation
and Air conditioning (HVAC) system, process
flow, etc. The operational challenges include sustainability,
seasonality or unavailability of raw materials,
and lack of scientifically validated quality control
methods for some rare ingredients. Recently, there is
a persistent perception that corporatization has shifted
its focus toward commercial gains at the expense
of quality. This scepticism highlights the need for
transparency in quality management practices and
regulatory compliance. By embedding Quality Management
System (QMS) within its operations, MSPCL
aims to address this concern, uphold the trust
of stakeholders, and set a benchmark for traditional
medicine manufacturing in the region.
This article provides a comprehensive overview of MSPCL’s efforts to mainstream QMS in its production processes. It examines key quality assurance mechanisms, sustainability practices in sourcing medicinal plants, personnel competency development, and the integration of regulatory frameworks. Furthermore, it discusses the challenges encountered and strategies employed to align TM production with global pharmaceutical standards without compromising traditional values. The reliance on traditional knowledge, variability of ingredients and dosage, and traditional practices contradict with the requirement of rigorous scientific validation, standardized quality control and dosage, and regulatory compliance.
METHODSThis article examines the implementation of Quality Management Systems at Menjong Sorig Pharmaceuticals Corporation Limited using a systematic approach to assess alignment with ISO 9001:2015 QMS standards and Good Manufacturing Practices. The methodology involves the evaluation of organizational practices in critical areas such as leadership and governance, risk management, supplier qualification, personnel training, process control, and documentation systems.
Data were gathered from primary sources, including Menjong Sorig’s Quality Manual version 4.0 (2024) and Site Master File version 07 (2024), which provide detailed insights into operational processes, quality control mechanisms, and compliance strategies. Secondary sources, such as WHO guidelines on GMP [5, 6] and good agricultural and collection practices (GACP) [1], were used to benchmark MSPCL’s practices against global standards. Relevant literature on Sowa Rigpa and traditional medicine practices in Bhutan [7, 8] supplemented the analysis by providing cultural and historical context.
The article also incorporated an in-depth review of MSPCL’s documentation, including batch records, supplier performance evaluations, personnel training logs, customer satisfaction surveys and internal audit reports. Key aspects of quality control such as product testing, risk-based decision-making, product quality review reports, and corrective and preventive action (CAPA) systems were examined to understand how MSPCL ensures the safety and efficacy of its products.
By focusing on these elements, the article provides a comprehensive assessment of how Menjong Sorig integrates ISO QMS standards and GMP principles into its operations, ensuring that traditional values are preserved while meeting modern pharmaceutical standards.
INTEGRATION OF QUALITY MANAGEMENT SYSTEMS
MSPCL’s Quality Management System (QMS) is meticulously designed to align with the principles of ISO 9001:2015 and Good Manufacturing Practices (GMP). These frameworks collectively ensure a systematic approach to the production of safe, effective, and high-quality traditional medicines. A Quality Manual outlines the organization’s quality policies, roles, and responsibilities with adherence to GMP principles as a core component [9, 10]. All production processes are standardized, documented, and supported by a system of periodic reviews and continuous improvement programs. Annual product quality reviews ensure alignment with regulatory submission and facilitate product optimization. To ensure the integrity of production, MSPCL conducts rigorous quality checks at multiple stages – from raw material sourcing to final product testing. Key functions, including Quality Control (QC), Quality Assurance (QA), and Production are managed by regulatory authority-certified competent professionals with background in GMP and quality assurance. There is good collaboration between QC/QA personnel and Drungtsho advisors – traditional medicine experts [8], and by embedding these principles into every stage of the production lifecycle, Menjong Sorig upholds its dual commitment to preserving the integrity of Bhutan’s traditional medicine practices and meeting modern pharmaceutical standards.
KEY COMPONENTS OF QUALITY MANAGEMENT SYSTEM
Figure 1 provides a high-level overview of the key components of the Quality Management System. Each component plays a crucial role in ensuring the quality and continuous improvement of products and services.
1. Leadership and Commitment
TIn line with the Clause 5 of ISO 9001:2015 standards, MSPCL's leadership demonstrates a strong commitment to quality by establishing a clear vision and defining roles and responsibilities. The top management plays an active role in the development and review of the quality-related policy, ensuring alignment with the organization’s strategic objectives [9, 10]. Regular management reviews are conducted to evaluate the effectiveness of the QMS and to implement improvements, reinforcing accountability and leadership's role in fostering a quality culture.
2. Customer Focus and Stakeholder Trust
A customer-centric approach, a hallmark of ISO 9001:2015, specifically Clauses 4.3, 5.2 and 7.2 underpins Menjong Sorig’s operations. As the sole provider of traditional medicines in Bhutan, Menjong Sorig recognizes the importance of meeting patient and stakeholder expectations. The customer satisfaction survey is conducted through professional third-party organisation on an annual basis and assessed against the customer satisfaction index benchmark. The integration of quality assurance measures and transparency in operations addresses concerns regarding corporatization and enhances trust in the organization’s ability to deliver high-quality products [8].
3. Risk-Based Thinking and Preventive ActionBoth ISO 9001 and GMP emphasize the importance of risk-based thinking. Menjong Sorig implements risk management strategies to identify, assess, and mitigate potential risks in the production process. For instance, sourcing medicinal plants involves carefully monitoring environmental and ecological risks, ensuring sustainable practices that minimize biodiversity loss [7]. Risk-based preventive actions extend to the supply chain, where supplier performance is continuously evaluated to ensure consistent quality.
4. Documentation and Change ManagementEffective documentation is a cornerstone of both ISO and GMP systems. MSPCL maintains a comprehensive three-tier document control system to ensure traceability and compliance with regulatory standards [9, 10]. Any changes to production processes or materials undergo a rigorous change management procedure, including risk assessments and corporatizaapprovals from quality assurance and regulatory authorities. This ensures that modifications do not compromise product quality or safety.
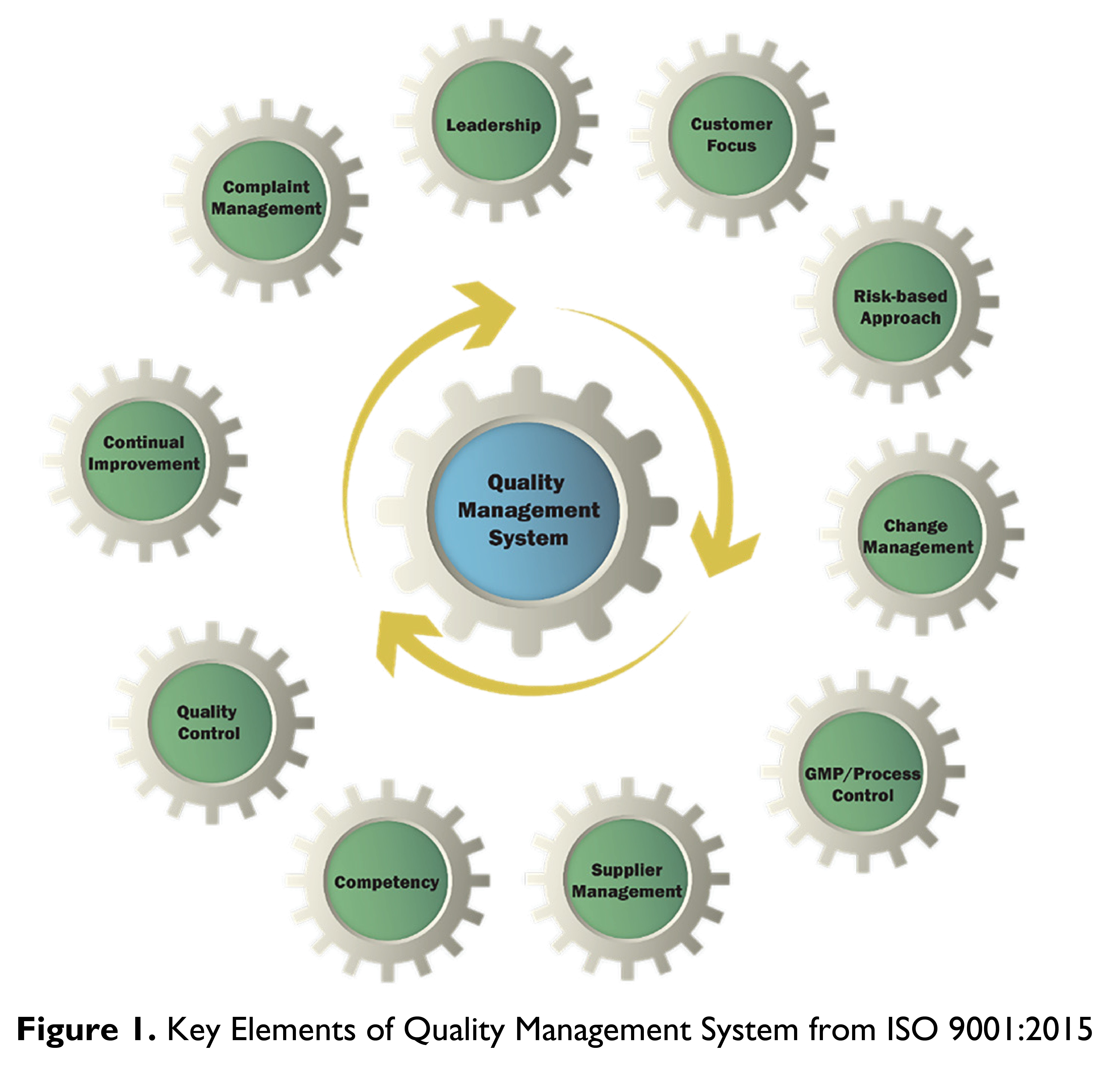
5. Good Manufacturing Practices (GMP) Principles
Adherence to GMP principles is evident in MSPCL’s approach to facility management, process control, and quality assurance. Key aspects include the following:
Facility ManagementMSPCL’s manufacturing premises, although not designed in full compliance with GMP requirements, features segregated areas for raw material storage, production, and quality testing. Regular environmental monitoring through third-party contract testing lab ensures a contamination-free production environment.
Process ControlEach stage of production, from preparation of raw materials to packaging, is governed by written SOPs and batch manufacturing records. In-process quality control mechanisms are in place to monitor critical parameters, ensuring consistent product quality [1].
Equipment Calibration and MaintenanceAll production equipment is routinely calibrated and maintained, with cleaning and maintenance records meticulously documented. Obsolete machinery is decommissioned following established protocols to maintain operational efficiency.
6. Supplier Qualification and Raw Material SourcingMSPCL’s QMS incorporates stringent supplier qualification processes to ensure the quality of raw materials. Approximately 85% of medicinal plant ingredients used in TM production are sourced locally, with most collected from the wild in Bhutan’s high-altitude regions (3500–5000 metres above sea level). Local farmers are trained in good collection practices and the sustainable harvesting of medicinal plants, as outlined in WHO’s guidelines on good agricultural and collection practices (GACP). The organization diversifies sourcing strategies by piloting the cultivation of high-demand herbs and encouraging the domestication of medicinal plants [7, 11].
7. Personnel Competency and TrainingISO and GMP frameworks stress the importance of skilled personnel. Menjong Sorig invests in continuous training programs for its staff, covering compliance to GMP, Good Laboratory Practices (GLP), and standard operating procedures (SOP). Exchange programs and international study visits provide exposure to advanced pharmaceutical technologies and practices. Regular performance evaluations ensure that employees meet competency standards and contribute effectively to quality objectives [9, 10].
8. Product Testing and Quality ControlMenjong Sorig’s Quality Control (QC) division conducts extensive testing on raw materials, intermediate products, and finished products to ensure they meet predefined quality parameters. Techniques such as High-Performance Thin-Layer Chromatography (HPTLC) and microbiological testing are employed to verify the identity, potency, and safety of products. QC processes align with ISO’s emphasis on evidence-based decision-making and GMP’s focus on product consistency and safety. The monograph publications on raw materials and finished products supported by other international pharmacopoeias guide the quality control process.
9. Continual Improvement and Self-AuditMenjong Sorig embraces ISO’s principle of continual improvement through regular internal audits or self-inspections, and management reviews. Observations from these inspections are addressed through corrective and preventive action (CAPA) plans. Semi-annual audits assess compliance with GMP and regulatory requirements, enabling MSPCL to identify gaps and implement enhancements to its QMS [1].
10. Complaint Management and Product Recall SystemA robust complaint management system is in place to address product defects and stakeholder concerns. All complaints are recorded, investigated, and resolved as per predefined procedures. Although MSPCL has no history of widespread product recalls, it maintains a comprehensive recall procedure to manage such incidents effectively, should they arise [9,10].
ADDRESSING CHALLENGES
Despite its adherence to ISO and GMP principles,
MSPCL faces challenges in public perception and
stakeholder trust. The concerns around corporatization and its potential impact on quality are mitigated
through transparent reporting and rigorous quality
assurance measures. By embedding ISO and GMP
principles into its QMS, Menjong Sorig not only reinforces
its credibility but also sets a benchmark for
traditional medicine manufacturing in Bhutan.
Key components of Menjong Sorig’s QMS, such
as robust documentation, supplier qualification, sustainable
raw material sourcing, and stringent quality
control measures, highlight the organization’s commitment
to producing high-quality traditional medicines.
Efforts to train personnel, implement risk
management strategies, and maintain compliance
with regulatory frameworks further strengthen the
reliability of its operations.
The integration of Quality Management Systems and Good Manufacturing Practices at MSPCL demonstrates a distinctive approach to harmonizing traditional medicine practices with modern pharmaceutical standards. By adopting ISO 9001:2015 principles, Menjong Sorig ensures a systematic focus on leadership, customer satisfaction, risk-based thinking, and continual improvement. Simultaneously, adherence to GMP principles reinforces product safety, efficacy, and consistency throughout the product’s lifecycle. These efforts reaffirm the organization’s role as a leader in traditional medicine manufacturing, setting a benchmark for balancing cultural heritage with scientific innovation.
Looking ahead, Menjong Sorig’s ongoing focus on sustainability, continual improvement, and alignment with these global standards positions it as a model for the integration of traditional medicine systems into contemporary healthcare frameworks. This approach not only safeguards Bhutan’s rich Sowa Rigpa heritage but also ensures that its traditional medicines remain safe, effective, and accessible to all.
Declarations
Ethics approval and consent to participate
Not applicable
Consent for publication
Not applicable
Competing interests
ST is a member of the editorial board of this journal. ST was blinded all processes related to peer review of this article.
Funding
There was no funding for this article.
Availability of data materials
All public sources of data have been cited in this article.
Author contributions
Conceptualization, Methodology, Data curation, Resources, Writing – original draft, Writing – review and editing: ST
Received: 28 November, 2024 Accepted: 01 March, 2025 Published online: 18 April, 2025
References
- World Health Organization. WHO guidelines on good agricultural and collection practices (GACP) for medicinal plants. Geneva; 2003. Available:https://iris.who.int/bitstream/handle/10665/42783/9241546271.pdf? sequence=1
- World Health Organization. WHO good manufacturing practices for pharmaceutical products: Main principles. WHO Technical Report Series, No 986, Annex 2 [Internet]. 2014 [cited 2025 Apr 14]. Available from: https://www.who.int/publications/m/item/trs986-annex2
- Ministry of Health, Royal Government of Bhutan. 5th National Health Survey: Integrated Stepwise Household Survey 2023. Thimphu, Bhutan: Ministry of Health; 2024. Available: https://moh.gov.bt/wp-content/ uploads/2025/01/Final_National-Health-Survey-2023-1.pdf
- Ministry of Health. Annual Health Bulletin 2019. Ministry of Health, Royal Government of Bhutan, Thimphu; 2019. Available: https://moh. gov.bt/wp-content/uploads/2025/01/AHB_2019.pdf
- World Health Organization. WHO Good Manufacturing Practices for the manufacture of herbal medicines. WHO Technical Report Series, No. 1010, Annex 1. Geneva: World Health Organization; 2018. Available: https://www.who.int/publications/m/item/trs1010-annex1
- World Health Organization. WHO Good Manufacturing Practices for the manufacture of herbal medicines. WHO Technical Report Series, No. 1010, Annex 2. Geneva: World Health Organization; 2018. Available: https://www.who.int/publications/m/item/trs1010-annex2
- Wangchuk D. State of Sowa Rigpa in Bhutan. Thimphu: National Institute of Traditional Medicine, Royal University of Bhutan; 2013. Available:https://www.ftm.edu.bt/wp-content/uploads/docs/TM%20Resources/ State%20of%20Sowa%20Rigpa%20in%20Bhutan.pdf
- Tenzin S. Collection of medicinal plants and production of traditional medicine. In: Bhutan-Japan Joint Symposium on the Conservation and Utilization of Medicinal Resources; 2006; Thimphu. Thimphu: Institute of Traditional Medicine Services (ITMS) and Bhutan Society for Conservation and Development of Himalayan Medicinal Resources (SCDHMR); 2006. Available: https://goto.now/pUS7K
- Menjong Sorig Pharmaceuticals Corporation Limited. Quality Manual, Version 4.0. Thimphu: Menjong Sorig Pharmaceuticals Corporation Limited; 2024.
- Menjong Sorig Pharmaceuticals Corporation Limited. Site Master File, Version 07. Thimphu: Menjong Sorig Pharmaceuticals Corporation Limited; 2024.
- Institute of Traditional Medicine Services. An introduction to Traditional Medicine services in Bhutan. Thimphu: Royal Government of Bhutan; 2010. Available: https://t.ly/wgaLN